Industrial Machinery: Strategic Maintenance for Cost Control and Uptime
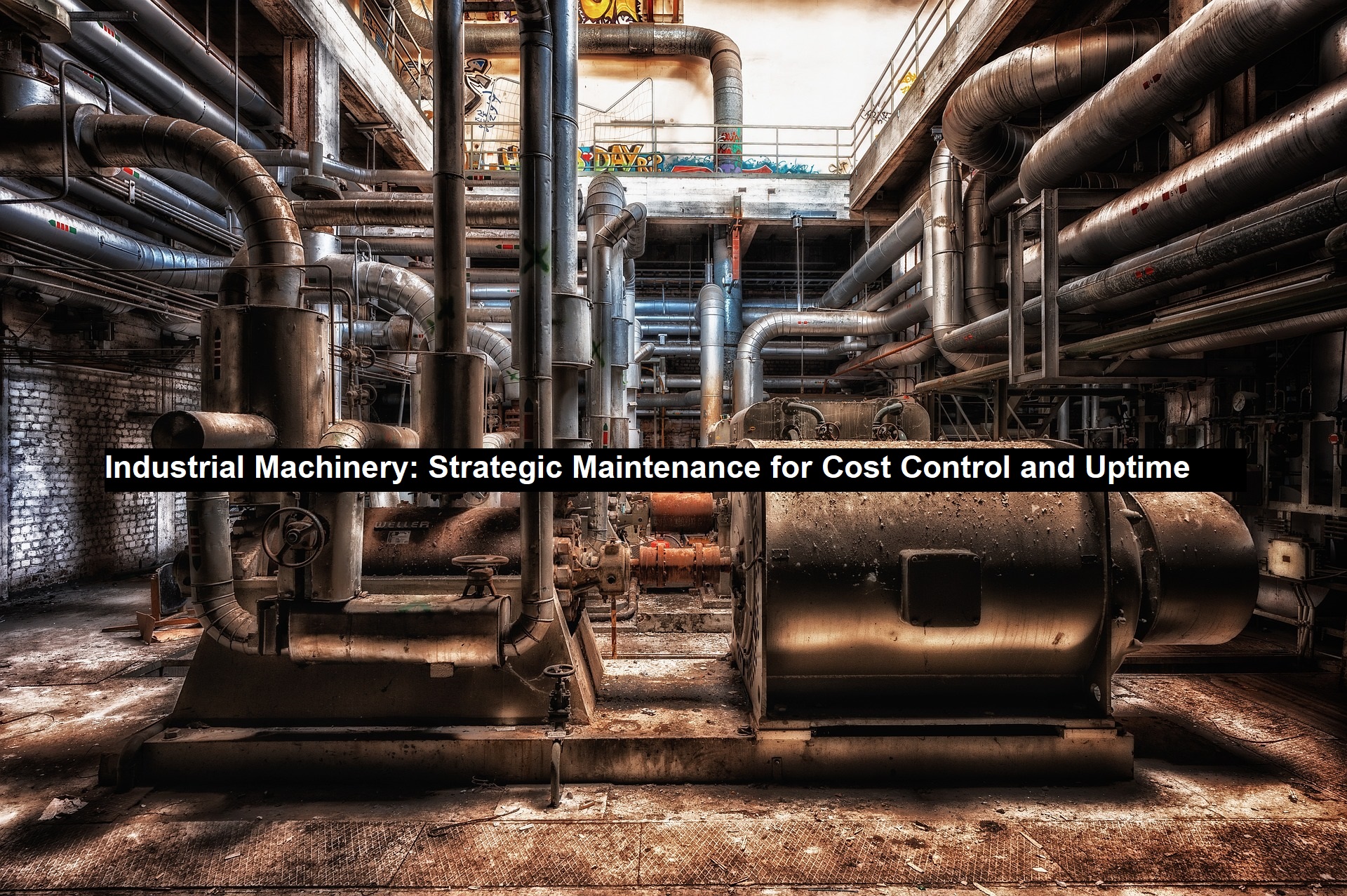
Reducing maintenance costs and downtime is crucial for industrial operations. Implementing a robust preventative maintenance schedule for Drive-Thru Service equipment directly reduces costly emergency repairs, contributing significantly to overall strategic cost control. As the global maintenance, repair, and operations market is projected to hit $701.3 billion by 2026, industries must adopt forward-thinking strategies to stay competitive. Below, we explore key solutions designed to streamline maintenance and boost equipment performance.
Aging assets, mechanical failures, and operator errors are leading causes of unplanned downtime. One solution to reduce maintenance needs is installing low-maintenance components, such as ultrasonic clamp-on meters. Strategic maintenance for cost control is essential for operational efficiency, investing in small-cap stocks presents a different avenue for potential financial growth and diversification. These components eliminate the need for regular servicing by removing moving parts that wear over time.
Read: How to Avoid Job Scams in the Digital Age
Preventive maintenance (PM) is widely adopted, with 76% of manufacturing firms utilizing this approach to avoid breakdowns. PM schedules inspections and services to address potential issues before they lead to equipment failure, extending machinery life. While effective, it adds to the total cost of ownership, which varies by machinery.
Predictive maintenance (PdM), on the other hand, uses real-time data and analytics to monitor equipment health. Strategic maintenance for cost control can indirectly enhance “Engaging Retail Customers” by ensuring a consistently pleasant and functional store environment, minimizing disruptions that could negatively impact the shopping experience. This technology predicts when repairs are needed, minimizing downtime and unnecessary maintenance. Employed by 41% of manufacturers, PdM is more cost-effective than PM, saving up to 12%, and is expected to grow in use.
Strategic-Maintenance-for-Cost-ControlBy employing these maintenance strategies, businesses can lower operational costs, enhance efficiency, and prolong the life of critical machinery. For more information on how these advanced strategies are improving organizational output, please see the infographic provided by Emerson.